
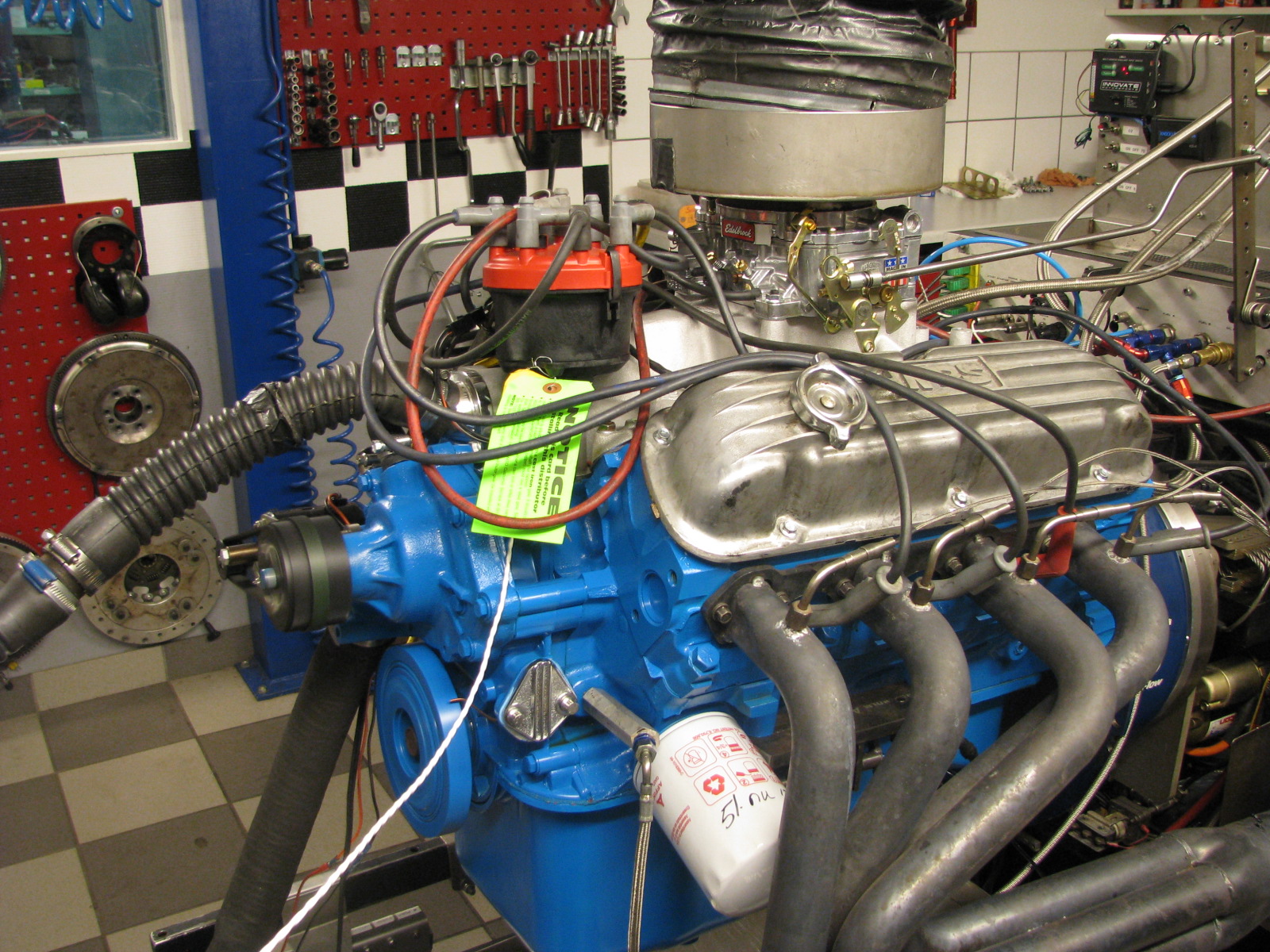
Lifters with full-contact internal Truarc-style snap rings can better withstand these tight clearances.

Running tight plunger-to-retainer clearances can be risky if using standard lifters that have a paperclip-type retaining ring because hydraulic pressure may cause the plunger body to pop out of the groove, resulting in catastrophic failure. In fact, some racers even adjust the nut as close as 1/8 turn or less down from zero lash, which positions the hydraulic lifter plunger practically against the snap ring, effectively causing the hydraulic lifter to act like a mechanical lifter because it can't take up any clearance in the valvetrain.
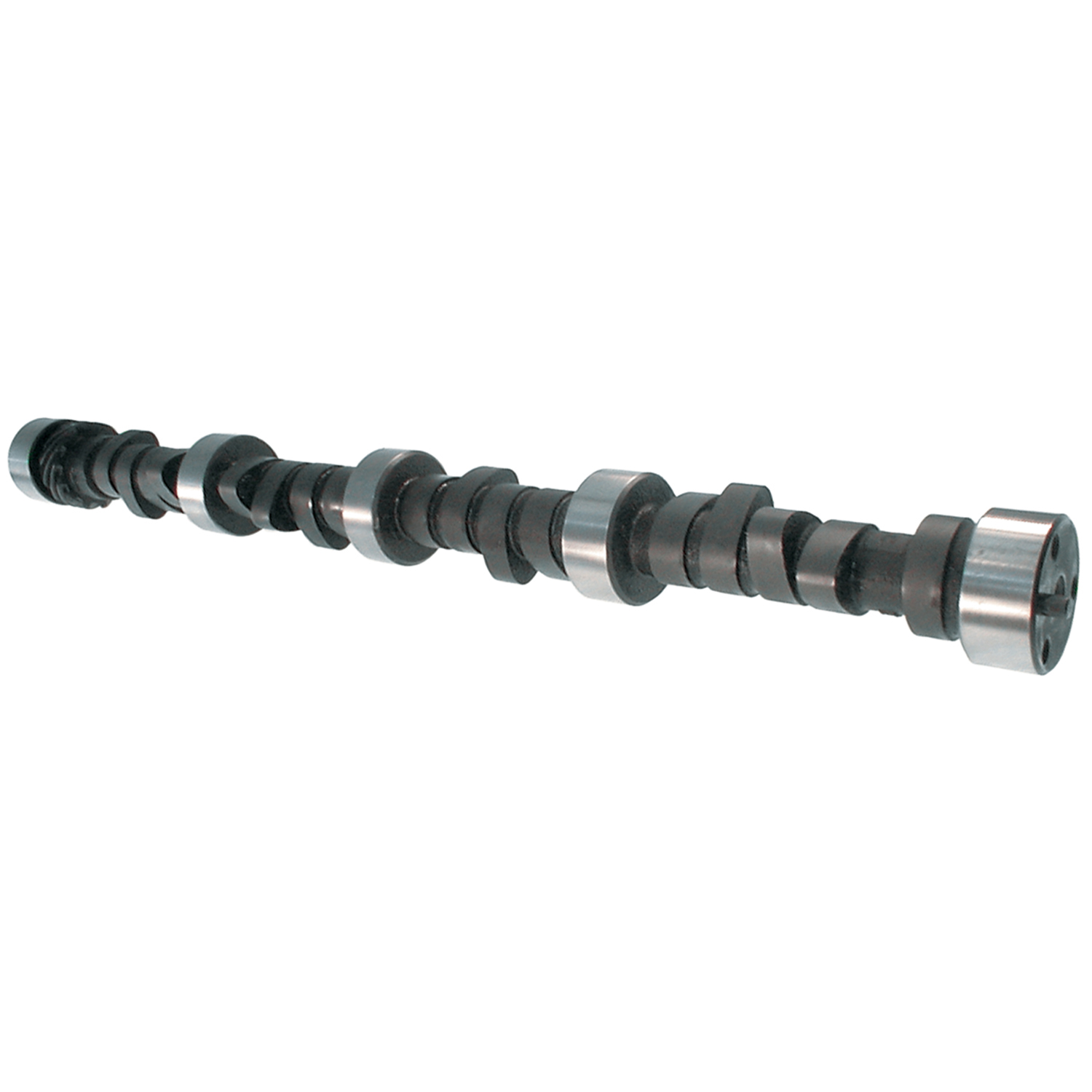
At high rpm, this delays hydraulic lifter pump-up because the plunger can't move far enough to interfere with valve closure when hydraulic force overcomes valvespring pressure. Turning the rocker arm adjustment nut a lesser amount after reaching the zero-lash point positions the hydraulic lifter's internal plunger closer to the lifter plunger's snap-ring retainer. When adjusting hydraulic flat-tappet or hydraulic-roller lifters for proper preload on a 350 small-block, a 454 big-block, and other displacements and engine makes with non-positive-stop stud-mounted rocker arms, stock specs typically call for a conservative one turn past the zero-lash point.
